Hydraulic Filtration: Full Pdf Version
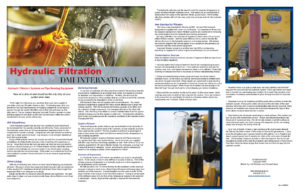

Hydraulic Filtration Systems on Pipe Bending Equipment
New oil is dirty oil and should be the only dirty oil your system ever sees.
That’s right, the mineral oil you purchase from your local supplier in your totes or in your 55 gallon drums is dirty. Purchasing clean oil is cost prohibitive for most manufacturers of hydraulic equipment. As the new oil passes through the system the filters will do their job and clean up that dirty new oil. Hence, properly designed hydraulic filtration systems on pipe bending equipment will clean up that dirty oil and bring it within the system requirements for your valves and pumps.
ISO Cleanliness
Every hydraulic system has an ideal ISO cleanliness level that should be maintained for it to operate correctly and efficiently. Every component in the hydraulic system has an ISO recommended cleanliness level for that component to operate correctly. Components with tight clearances between parts (ie: a valve spool and body) may require a more stringent cleanliness level than a gear pump.
Using a fluid analysis service will provide you with the concentration levels of Additives, the Total Acidity Number of the oil and the ISO cleanliness of the oil. These three items will help you make an informed decision whether or not you should change your oil. A fluid analysis will also report the amount of water in the hydraulic oil. Excessive water in the oil will cause foaming, reduce viscosity and excessive wear. While water is a contaminant found in many hydraulic systems I have not found it to be an issue on pipe bending equipment.
Silver Lining
With all of that being said, there is a silver lining to keeping your hydraulic oil clean. Research shows that equipment which operates with oil maintained to the required ISO cleanliness level will last at least three times longer than equipment that is not designed accordingly.
Longer service life is a value we strive to provide our customers. We take extra steps to clean our new oil and provide three micron filtration in all of our new equipment.
Servicing Intervals
In my post on hydraulic oil I discussed how hydraulic oil servicing intervals should not be established at an arbitrary time frame, but should be checked for depletion and degradation of additives. Similarly, the oil should be checked for cleanliness. Wear particles that are not filtered out of the hydraulic oil can accelerate the degradation of the oil additives.
DMI hydraulic filters are all supplied with visual indicators. Our newly designed equipment is supplied with three micron filtration and a larger dirt holding capacity. With the increased dirt holding capacity of our filters and the reduction of ingression points, the changing intervals of the filters will extend. The efficiency of the filters to remove contamination from the system actually increases as the filter begins to collect dirt. Consideration should be given to the oil cleanliness and the operating conditions of the machine before changing the filter.
System Failures
Almost all hydraulic system failures can be attributed to dirty hydraulic oil. So, where does the contamination in the hydraulic system originate and how does it get into the system? The fine powdery dust found on most right of ways is the number one culprit and there are several points of ingression on pipe bending equipment.
All hydraulic systems require a hydraulic reservoir and these reservoirs are supplied with filler caps and breathers. Some reservoirs are supplied with filler caps that have breathing capability as well. Both of these items are typically supplied with 40 micron filtration levels. For reference, a human hair is about 40 micron in diameter. Hence, selecting the correct components based on the working condition of the equipment is critical.
Sources of Ingression
In a hydraulic system, a 40 micron size particle can cause a catastrophic failure. It can cause a valve to stop shifting or a pump to lock up. One of the primary sources of ingression in a hydraulic system on mobile equipment is the air breathers on the reservoir.
At DMI we utilize 5 to 10 micron filtration for the breathers on the reservoir because 5 micron is much more efficient than 40 micron at keeping large dust particles out of the reservoir. A large breather must be used in order for the large volumes of air to pass in and out of the reservoir. During a normal cycle of the Stiffback circuit 25% to 35% of the hydraulic oil volume in the reservoir is exchanged. Hence, large air flow capacity is required for the reservoir breathers.
The hydraulic cylinders are the second culprit for sources of ingression in a pipe bending machine hydraulic circuit. Rod wipers do an excellent job of keeping the rods clean as the cylinders stroke up and down. Unfortunately, ultra fine particles still find their way under the rod wiper and into the hydraulic system.
New Standard for Filtration
We have a new standard for filtration at DMI. All new DMI designed equipment is supplied with three micron filtration. Our experience shows that the industry standard ten micron filtration systems are insufficient in removing the contamination found in hydraulic pipe bending equipment.
Similarly, DMI filters the hydraulic oil supplied in drums with a three micron offline filtration system. And the same filtration cart is used to transfer the oil from the drum to the hydraulic reservoir on the pipe bender. We believe this process improves the roll out quality of our equipment and provides our customers with the most reliable equipment.
Improved filtration systems is another way that DMI is continuously improving its equipment to deliver improved performance to our customers.
Contamination Sources
Here we address the most common sources of ingression that we have found in pipe bending equipment.
- Particles exist in the hydraulic reservoir due to the manufacturing process that are not adequately cleaned out. These particles work their way into the systems over time. Just wiping the reservoir clean is not sufficient. Chemically cleaning a hydraulic reservoir is necessary to remove manufacturing residue.
- During the manufacturing process plugs and caps should be used on hydraulic hoses. As the hoses are stored, moved and installed contaminants can enter the open hose ends. When repairs are performed on pipe bending equipment and hoses are temporarily removed or if hoses are stored on a rack the end should be plugged. When hoses are installed, the best practice is to blow felt “pigs” through the hose for a final cleaning just before installation.
- Wear particles are created mostly by the pump. As the pump wears, metal shavings can come off and find their way into the system. There are surfaces in the pump that are specifically designed as a bearing surface where two metal pieces are in contact. These surfaces wear.
- Anywhere there is a seal (ie shaft seal, rod seal) particles can find their way past the seal and into the hydraulic system. Seals age harden and wear due to normal use, overheating and sunlight. As a result they become more susceptible to allowing contamination to pass through and into the hydraulic system.
- Openings such as air breathers and filling ports allow particles to enter the hydraulic system. These ports collect dirt around the perimeter of the seal opening. When the port is opened contamination falls into the reservoir. Many reservoir air breathers are coarse wire mesh and designed for high air flow which allows contamination into the reservoir.
- Over heating the oil causes varnishing on metal surfaces. This varnish can peel off as a new contaminate as well. Proper operating temperatures are discussed in a previous blog. Hot oil not only creates a varnish surface on metal and brass parts, but it also changes the properties of the oil creating sludge and changes the acidity of the oil.
- As a “rule of thumb” it takes 7 tank volumes of the fluid to pass through the filter for the filter to reach 100% of the oil. For an 80 gal reservoir, 1 pass would be 80 gallons and 7 passes would be 560 gallons. For a 70 gallon per minute pump it would take 8 minutes for 100% of the oil to pass through the filter. Unfortunately, there are pockets of oil in the reservoir that do not get circulated as easily as the main fluid channel and silting occurs in these areas. Over time silting becomes sludge that breaks free and finds its way into the hydraulic system.