Hydraulic Filtration: Seven things you should know about hydraulic oil contamination
Seven things you should know about hydraulic oil contamination
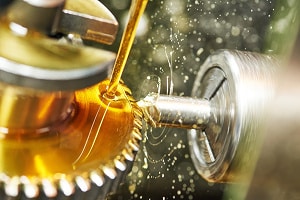
New oil is dirty oil and should be the only dirty oil your system ever sees.
As you know from our previous article, the mineral oil you purchase from your local supplier in your totes or in your 55 gallon drums is dirty and the oil in your system has continuous sources of contamination ingression. This article addresses the most common sources of ingression in pipe bending equipment.
- Particles exist in the hydraulic reservoir due to the manufacturing process that are not adequately cleaned out. These particles work their way into the systems over time. Just wiping the reservoir clean is not sufficient. Chemically cleaning a hydraulic reservoir is necessary to remove manufacturing residue.
- During the manufacturing process plugs and caps should be used on hydraulic hoses. As the hoses are stored, moved and installed contaminants can enter the open hose ends. When repairs are performed on pipe bending equipment and hoses are temporarily removed or if hoses are stored on a rack the end should be plugged. When hoses are installed, the best practice is to blow felt “pigs” through the hose for a final cleaning just before installation.
- Wear particles are created mostly by the pump. As the pump wears, metal shavings can come off and find their way into the system. There are surfaces in the pump that are specifically designed as a bearing surface where two metal pieces are in contact. These surfaces wear.
- Anywhere there is a seal (ie shaft seal, rod seal) particles can find their way past the seal and into the hydraulic system. Seals age harden and wear due to normal use, overheating and sunlight. As a result they become more susceptible to allowing contamination to pass through and into the hydraulic system.
- Openings such as air breathers and filling ports allow particles to enter the hydraulic system. These ports collect dirt around the perimeter of the seal opening. When the port is opened contamination falls into the reservoir. Many reservoir air breathers are coarse wire mesh and designed for high air flow which allows contamination into the reservoir.
- Over heating the oil causes varnishing on metal surfaces. This varnish can peel off as a new contaminate as well. Proper operating temperatures are discussed in a previous blog. Hot oil not only creates a varnish surface on metal and brass parts, but it also changes the properties of the oil creating sludge and changes the acidity of the oil.
- As a “rule of thumb” it takes 7 tank volumes of the fluid to pass through the filter for the filter to reach 100% of the oil. For an 80 gal reservoir, 1 pass would be 80 gallons and 7 passes would be 560 gallons. For a 70 gallon per minute pump it would take 8 minutes for 100% of the oil to pass through the filter. Unfortunately, there are pockets of oil in the reservoir that do not get circulated as easily as the main fluid channel and silting occurs in these areas. Over time silting becomes sludge that breaks free and finds its way into the hydraulic system.