Hydraulic Oil: Full Pdf Version
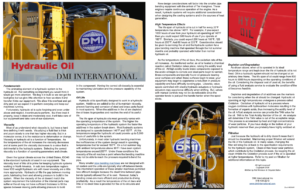
Hydraulic Oil
Fundamentals
The animating element of a hydraulic system is the hydraulic oil. For something so important you would think it would get more attention. We buy it in bulk so we can get the best price but we give little attention to how we store it and transfer it into our equipment. We allow it to overheat and get dirty and yet we expect it to perform everyday and keep our machines running.
Fortunately, hydraulic oil is quite forgiving and even under abuse and neglect, it continues to perform. But if we treat it properly, keep it clean and moderately cool, it will take care of our equipment and take care of our customers.
Viscosity
Most of us understand what viscosity is, but have a hard time defining it with words. Visualizing a fluid that is thick and pours slowly is one that has higher viscosity. But in a molecular sense, it is the resistance to deformation or change. Viscosity in hydraulic oil is a function of Temperature. As the temperature of the oil increases the viscosity decreases and at some point the viscosity decreases to a value that is detrimental to the hydraulic system. Selecting the correct viscosity is a function of operating parameters and climate.
Given the typical climate across the United States, ISO46 is the standard hydraulic oil used in our equipment. The viscosity level of this oil is prime for keeping hydraulic systems working in North America. In sub zero temperature regions lower IOS weight hydraulic oils with lower viscosity are a little more appropriate. Hydraulic oil fills the gap between moving parts; lubricating them and allowing pressure to build in the system. When the viscosity of the oil doesn’t match the system requirement the lubrication of the internal parts may suffer or the oil may not have sufficient thickness to fill the spaces between moving parts allowing pressure to build in the component. Having the correct oil viscosity is essential to maintaining lubrication and the pressure capability of the system.
Oil Life
Hydraulic oil is specifically designed to work in a hydraulic system. Additives are added to the oil to maintain viscosity, prevent foaming and corrosion of steel and brass parts found in most systems. When the additives in the oil are depleted the oil loses its properties and reaches the end of its oil life.
The life span of hydraulic oil most generally varies with the operating temperature of the system. The higher the operating temperature of the hydraulic system the faster the additives in the system break down. Most hydraulic systems are designed to operate between 140°F and 160°F. At this temperature range the hydraulic oil could provide up to 5,000 hours of useful life to the system.
Unfortunately, in most older hydraulic bending machines the inefficiencies of the system design result in operating temperatures that far exceed 160°F. On a hot summer day with ambient temperatures above 95°F, I have seen system temperatures exceed 250°F. Under these conditions the viscosity of the oil reaches a point where the bending machine may not be able to reach the pressure required to bend the pipe.
Many smaller pipe bending machines are not designed with oil coolers and the units are typically shut off between bends. The intermittent operation of these smaller machines permitted less efficient designs because the dwell time between pipe bends typically allowed the oil to cool. However, today’s bending crews are more efficient and production is driving profitability. As a result the temperature of the oil rises and little or no dwell time is provided for the oil to circulate and cool.
New design considerations will factor into the smaller pipe bending equipment with the arrival of Tier 4 engines. These engines require continuous operation of the engine. As a result, hydraulic systems will require additional consideration when designing the cooling systems and in the sources of heat generation.
High Temperature Effects
The life span of hydraulic oil is cut in half for every 20°F temperature rise above 140°F. For example, if you expect 1000 hours of use from your hydraulic oil operating at 140°F then you could expect 500 hours of use if you operate at 160°F. Similarly, you could expect 250 hours at 180°F; 125 hours at 200°F; And 60 hours at 220°F. Consideration should be given to servicing the oil and the hydraulic system for a pipe bending machine that operated through the hot summer months and probably operated with hotter than normal hydraulic oil.
As the temperature of the oil rises, the oxidation rate of the oil increases. As mentioned earlier, as oil is heated a chemical reaction called Oxidation takes place, raising the acidity level of the oil. At high acidity levels brass components exposed to the acidic oil begin to corrode and steel parts begin to varnish. Brass components are typically found on pressure bearing wear surfaces and when these surfaces begin to wear, your equipment may begin to experience a reduction in pressure capability and have difficulty bending pipe. Likewise, valve spools controlled with electro-hydraulic actuators or hydraulic actuators may experience difficulty when shifting. But, valves with manual controls may not be as noticeable since the operator tends to just pull the handle harder when the spool sticks.
Depletion and Degradation
As shown above, when oil is operated in its ideal temperature range and kept clean the life of hydraulic oil is not fixed. Oil in a hydraulic system should not be changed at an arbitrary time frame. The life span of oil could range from 500 hours to 5000 hours depending on the operating conditions of the oil. Considering the disposal cost of used oil, the benefits of using a fluid analysis service to evaluate the condition of the oil becomes feasible.
Depletion and degradation of oil additives are the markers for considering when the oil should be changed. Hydraulic oil operating at high temperatures undergoes a process called Oxidation. Oxidation of hydraulic oil is a process where oxygen combines with hydrocarbon molecules resulting in the formation of organic acids, thus increasing the acidity level of the oil. A fluid analysis service can provide the TAN value for the oil. TAN is the Total Acidity Number of the oil. An analysis will determine if the TAN value is out of the acceptable range. This process is accelerated by heat and high concentrations of wear particles. If you have sludge in the bottom of your hydraulic reservoir then you probably have highly oxidized oil.
Filtration
Just because the hydraulic oil is dirty doesn’t mean that it should be discarded. Maintaining proper filtration will extend the life of the hydraulic oil. In many cases, changing the filter will bring the oil back to the specification requirements for the hydraulic system. Clean oil has fewer wear particles which contribute to the Oxidation process. So keeping the oil clean inhibits the Oxidation process even if the oil is operated at higher temperatures. Refer to my post on filtration for additional information on this topic.
Written by Pat Kinnison & Chrystal Bates
All rights reserved
Copyright 2020
Pat Kinnison, CFPHS, CFPHCS; is Vice President of Engineering at DMI International, Inc. He has over 30 years of experience working in the fluid power industry in control systems and mechanical design as well national and international sales management.
Chrystal Bates, is Director of Marketing as well as Executive Assistant to the President at DMI International, Inc. Her marketing responsibilities include but are not limited too; catalogs, brochures, website and SEO management as well as editor and creative layout for published content.